2021 Biomass Pelletizer Technology Research and Future Development Trend Analysis
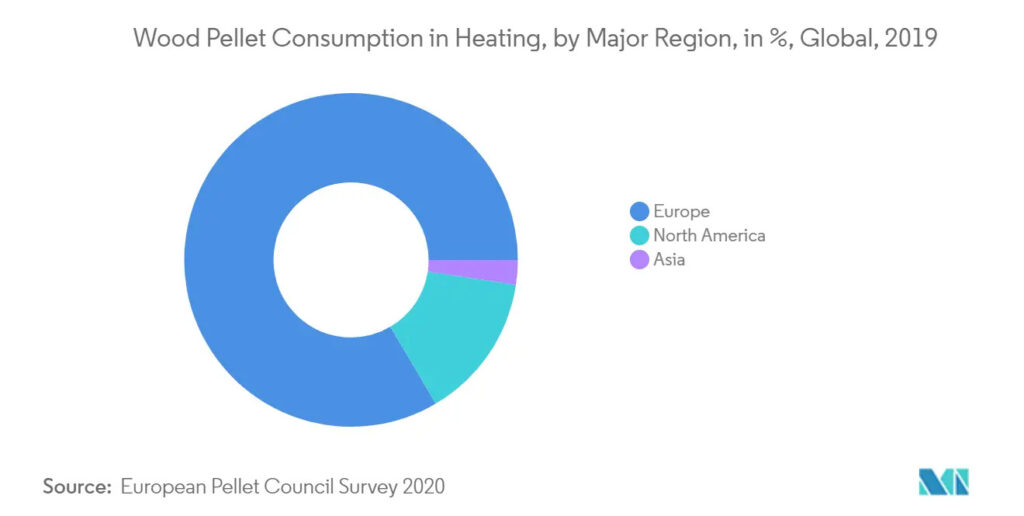
Mainstream Product Technical Route
According to the different layout of the pelletizing ring die, it can be divided into vertical pelletizer and horizontal pelletizer. RICHI Machinery is a horizontal biomass pelletizer.
The working principle of the biomass pelletizer is to use the extrusion and friction force generated during the movement of the ring die and the pressure roller (or ring die) to remove straw, wood chips or rice husks in the pelletizing cavity under high temperature and high pressure. It is compacted and extruded out of the die hole, and finally a regular, denser molding fuel is formed.
The pelletizing ring die and pressure roller are the core components of the biomass pelletizer. The mainstream technology mainly adopts the single ring die + double pressure roller (three pressure rollers) method. According to the layout of the ring die and material feeding relative to the whole machine, it is divided into vertical and Two types of horizontal. The powder material of the vertical granulator is fed into the granulation cavity from the upper part of the whole pellet machine, and the ring die is placed horizontally relative to the granulation unit; the powder material of the horizontal granulator is fed vertically from the front end of the granulation cavity (with the help of the fan Forced feeding), the ring die and the pelletizing unit are arranged vertically.
Classification of Biomass Pelletizer Types
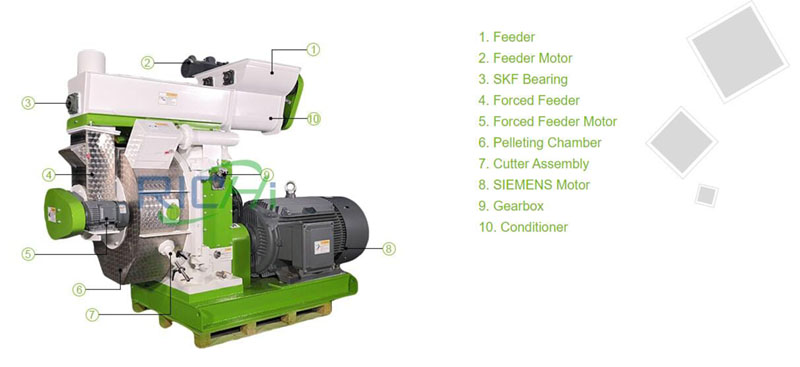
In the international and domestic markets, the power drive of biomass pelletizers is generally completed by motors, and the equipment is mainly fixed. The working position of the fixed granulator is relatively fixed, and the granulation operation is generally completed in the workshop. The high-efficiency granulator unit is often equipped with shredding, conveying, dust removal, cooling and packaging systems, which operate in a production line. The power source is generally a motor, and motors of different powers are selected according to the efficiency of the production line or equipment.
At present, the pelletizers in the international and domestic markets are mainly fixed types. The products of various manufacturers have differences in the core working component structure, the technical route of the whole machine, and the design of product work efficiency, and the reliability of similar products has a large gap. In order to pursue profit, some pelletizer manufacturers have relatively short service life of the ring die and press roller. Generally, they need to be replaced when processing about 1000t (some manufacturers need to replace about 500t). The frequency of maintenance and replacement is high, which makes the manufacturing The cost of using the granulator remains high.
Theoretical Analysis of Pelletizing
Straw and other materials contain a certain amount of cellulose and lignin. The lignin is a structural monomer in the material and is a phenylpropane-type polymer compound. It has the function of strengthening cell wall and binding cellulose. Lignin is non-crystalline, the main part is insoluble in any solvent at room temperature, has no melting point, but has a softening point. When the temperature reaches a certain value, the softening and cohesive force of lignin will increase, and under certain action, the cellulose molecular cluster will be dislocated, deformed and stretched. The adjacent biomass particles in the interior will engage each other, recombine and be pressed into shape.
The biomass pelletizer uses mechanical force (extrusion force, friction force, etc.) to compact and squeeze straw, wood chips or rice husk out of the die hole under high temperature and high pressure environment, making full use of lignin or fiber during the process. The high-temperature bonding effect of the element will eventually compress the biomass powder into granular materials.
Biomass ring die pelletizing technology is an advanced pelletizing technology that integrates multidisciplinary knowledge such as mechanical engineering and powder mechanics. In the process of pressing biomass particles, it is essentially a process in which the material is deformed by the combined action of squeezing force, friction force, and high temperature and high pressure.
According to the different states of the powder in the granulation and molding process, the whole process can be divided into 3 areas: feeding area, deformation and compression area and extrusion forming area, as shown in the figure below.
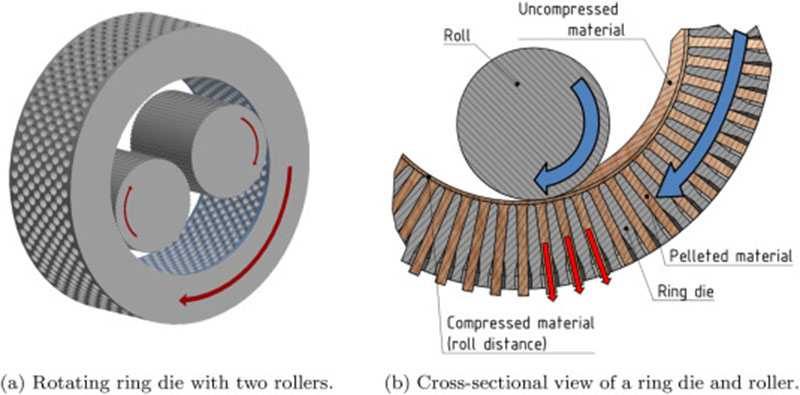
Feeding area: The material is basically not subject to squeezing force, but centrifugal force will be generated during the rotation of the ring die. Under the action of the centrifugal force, the powder material is tightly attached to the inner side of the ring die.
Deformation compaction zone: With the rotation of the outer ring die, the pressure roller simultaneously rotates passively. The material enters the compaction zone under the action of the ring die, and is simultaneously squeezed and rubbed by the ring die and the pressure roller, resulting in relative movement between the materials . As the material moves forward, the squeezing force gradually increases, the gap between the powder particles gradually becomes smaller, resulting in deformation, and the density of the material gradually increases.
Extrusion molding area: When the material enters this area, the extrusion force and friction force increase rapidly, and at the same time, a high temperature and high pressure environment is generated. The contact area between the materials increases, and the mutual bonding occurs under the action of lignin and cellulose. It is continuously squeezed into the die hole to form particles of different densities. In the squeezing zone, the gap between the ring die and the pressure roller will be 0.5~1.0mm. With the wear of the ring die and the pressure roller during the granulation process, the gap between the two will gradually increase. When a certain limit is exceeded (the general experience is 5mm) The granulation effect will be affected, and the ring die and pressure roller need to be adjusted or replaced.
Judging the Future Development Trend of Industry Technology
According to the development history and technical status of the biomass pelletizer industry, and with reference to the comprehensive analysis and judgment of the technological development history of international high-end brands, the technical field of biomass granulators will mainly develop in the following aspects in the future.
- Gradually build a complete technical system, including pelletizing technology, core component design, manufacturing technology, new materials and intelligent control, etc.
At present, some developed countries have formed a sound ring-molded pelletizing equipment technology system, which can provide a variety of high-quality and efficient production equipment and complete engineering solutions. Internationally renowned ring die biomass pellet machine companies have carried out systematic research on granulating technology, equipment design and manufacturing, intelligent control technology, expert diagnosis and service technology, etc., and formed a complete technical system. - Continuously optimize and improve core component technologies such as ring die and pressure roller, including optimization and adjustment of technical parameters, application of new materials, improvement of heat treatment process, optimization of die hole structure and technical parameters, etc., effectively improve the adaptability and service life of core components, and increase manufacturing The performance, reliability and work efficiency of the biomass pelletizer.
- Towards large-scale and intelligent development. Continuously introduce intelligent control technology to continuously improve the intelligent monitoring and operation level of the equipment, thereby improving the overall technical level of the ring die biomass pelletizing equipment.
- Continuous optimization of the process flow of the biomass pellet production line, the development of an intelligent whole-process monitoring and management system, realizing the constant monitoring, adjustment and fault diagnosis of the production line, and gradually realizing automatic operation.
- The mobile granulation technology continues to mature, and the system compatibility of various functional components is gradually improved. Gradually applied in crop straw field granulation, the adaptability of the core granulation unit to crop straw moisture and morphology has been continuously improved, and the technology of the whole machine has gradually matured. The mobile granulator will be an innovative product of the pelletizer in the future, and the fixed granulator will jointly promote the continuous maturity and development of the technology and products of the biomass pelletizer industry.
Pellet Production Line
Core Equipment of Wood Pellet Production Line
RICHI Pellet Machine For Sale
- Wood Pellet Mill For Sale
- Grass Pellet Making Machine For Sale
- Straw Pellet Machine For Sale
- Rice Husk Pellet Machine For Sale
- EFB Pellet Machine For Sale
- Organic Fertilizer Pellet Machine For Sale
- Cat Litter Pellet Making Machine For Sale
- Textile Cord Pellet Machine For Sale
- Paper Pellet Making Machine For Sale
- Pellet Maker For Pellet Stove