Design and Maintenance of Wood Pellet Machine Mould
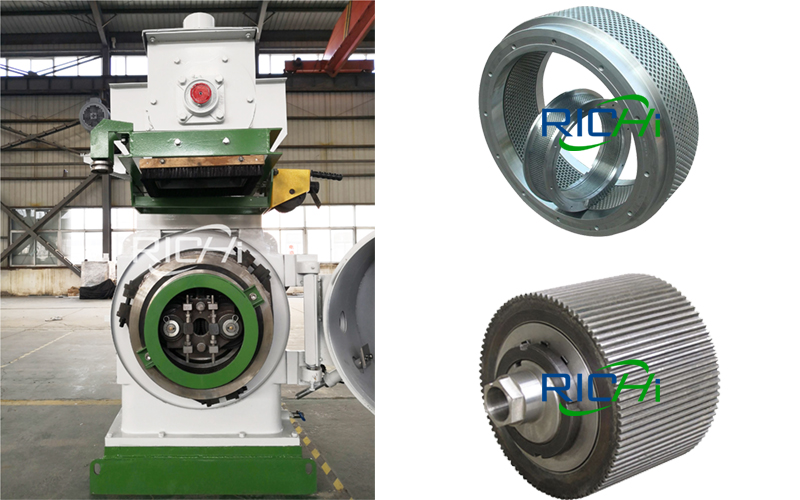
As the core component, design of the wood pellet machine mould has a great impact on improving the output and quality of wood pellet production, reducing energy consumption, and reducing production costs.
At the same time, the wood pellet machine mold is also one of the most easily worn parts. Therefore, it is very important for wood pellets producers to understand the design and application of ring die, and to make correct selection, rational use and effective maintenance of ring die.
The following is a brief analysis of the design, selection, use and maintenance of the ring die for reference.
1, Determination of ring die diameter and ring die effective pressing width parameters
a, The diameter and effective width of the ring die are the main parameters of the wood pellet machine die
According to the international wood pellet machine parameters and priority sequence to determine the ring die diameter series, RICHI mainly has the following series of wood pellet machines:
- MZLH320 Wood Pellet Machine
- MZLH350 Wood Pellet Making Machine
- MZLH420 Wood Pellet Mill
- MZLH520 Wood Pellet Maker
- MZLH768 Wood Pellet Press
- MZLH858 Wood Pelletizer
According to the ratio of equal effective pressing area and equal power, determine the effective width of the ring die.
b, Determination of the rotational speed of the press roller of the wood pellet machine
The rotational speed of the press roller is related to the geometric parameters of the wood pellet machine itself. According to the data detection of the technical parameters of the international pellet machine, for the ring die pellet machine with two pressing rollers, the linear speed at the inner diameter of the ring die is 6-12m/s is more suitable. This is also the difference between the speed of the sawdust pellet machine and the feed pellet machine.
The speed of the roller of the wood pellet machine directly affects the thickness of the material in the pelletizing chamber and the time for the material to pass through the die hole, which in turn affects the output of the pellet machine and the quality of the pellets. If the line speed is too high, under the same output, the ring die produces less particles per revolution, and the material in the granulation room is small and unevenly distributed, which may cause material faults, discontinuous granulation, loose particles with different lengths, and a large amount of powder. Can’t even granulate. A lower ring die line speed can produce pellets and can produce higher quality pellets, but the throughput is relatively low.
c, Determination of the diameter of the pressing roller
The basic pelletizing principle for pellet formation is shown in the figure below. The wood pellets can overcome the resistance of the material passing through the aperture of the ring die through the mutual extrusion force between the ring die and the pressing roller, so as to achieve the purpose of granulation.
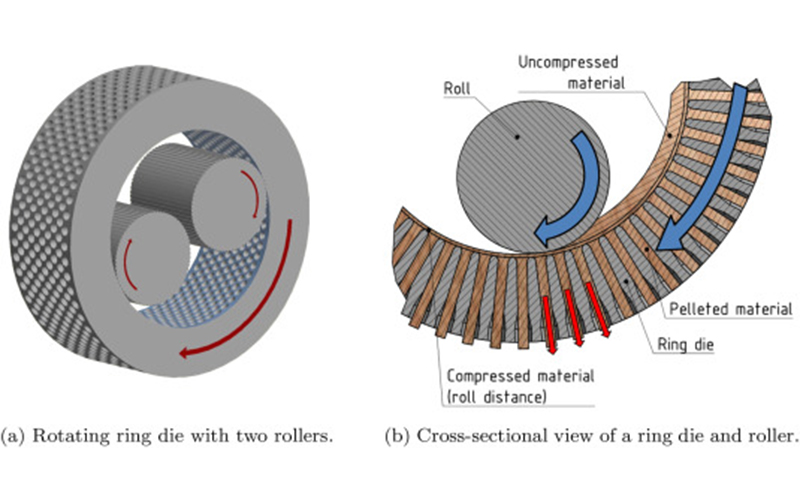
Under the same ring die, the larger the diameter of the pressure roller, the greater the range of triangular extrusion formed between the ring die and the pressure roller, which is more conducive to the extrusion effect.
Theoretically speaking, the diameter of the pressure roller of a single roller can be the largest, and the extrusion time and extrusion effect should be the best. However, in the operation of the wood pellet mill, the most force between the pressing roller and the ring die is transmitted between the main shaft, the bearing and the empty shaft, so the mechanical structure of the single-roller granulator is coarse, so it can only be used on a small experimental granulator. It is difficult to be used in large-scale pellet mills, and the double-roller sawdust pellet mill has become the most used model in pellet.
2. Ring die material and heat treatment
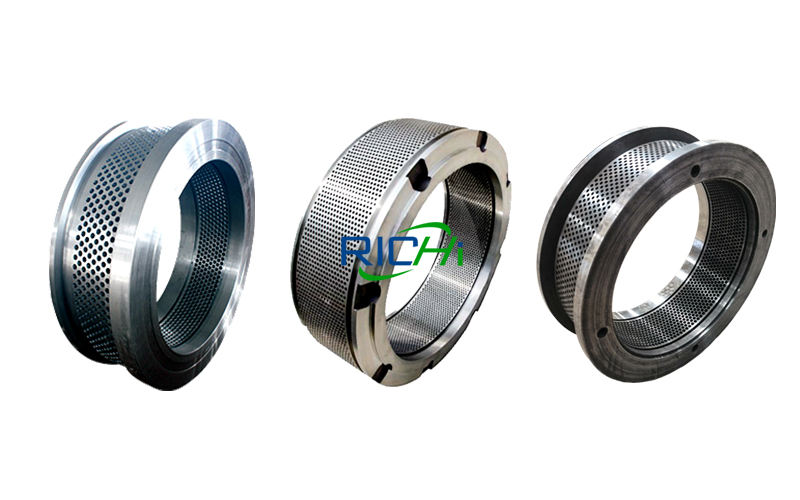
Wood pellet machine moulds are usually made of carbon steel, alloy steel and stainless steel through forging, cutting, drilling, heat treatment and other processes. The material used in the ring die and each processing procedure have a direct impact on its service life, granulation quality and output.
- Carbon Steel – Heat Treated Hardness HRC45-50. The wear resistance and corrosion resistance are relatively poor and are basically eliminated.
- Alloy Steel – Heat treated with hardness above HRC50. The comprehensive mechanical properties are high, and the utilization rate is the highest.
- Stainless Steel – Good hardness and toughness, overall quenching, and good wear and corrosion resistance. But its high price has dragged down overall usage.
3. Ring die hole structure, compression ratio
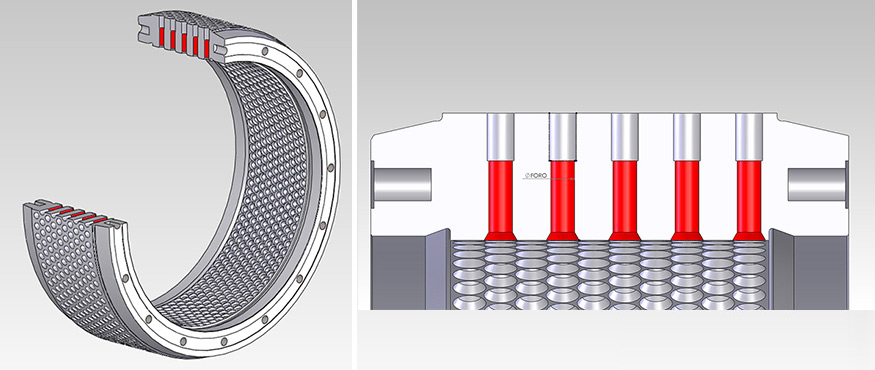
Common wood pellet machine moulds have straight holes, decompression holes, outer tapered holes and inner tapered holes. The main parameters are:
Die hole diameter, ring die thickness, ring die effective thickness, decompression hole length, die hole center distance, wall thickness between die holes, ring die diameter, ring die effective width.
The compression ratio is the ratio of the effective thickness of the ring die to the diameter of the die hole. It is an indicator of the extrusion strength of wood pellets. The higher the compression ratio, the stronger the extruded particles. Therefore, the die hole of the ring die is determined according to the different raw materials of wood.
4. Use and maintenance of wood pellet machine mould
Correct adjustment of the working gap between the ring die and the pressing roller is the key to the use of the ring die. Generally speaking, the gap between the ring die and the pressing roller is between 0.1-0.3mm.
When the gap is too large, the machine will be blocked due to insufficient extrusion force. If the gap is too small, it is easy to damage the ring die and the pressing roller. For the operator, it is necessary to have practical operation experience and be able to skillfully select and adjust the gap of the ring die roll. The adjustment work needs to be mastered through long-term granulator production practice.
Pellet Production Line
Core Equipment of Wood Pellet Production Line
RICHI Pellet Machine For Sale
- Wood Pellet Mill For Sale
- Grass Pellet Making Machine For Sale
- Straw Pellet Machine For Sale
- Rice Husk Pellet Machine For Sale
- EFB Pellet Machine For Sale
- Organic Fertilizer Pellet Machine For Sale
- Cat Litter Pellet Making Machine For Sale
- Textile Cord Pellet Machine For Sale
- Paper Pellet Making Machine For Sale
- Pellet Maker For Pellet Stove