Why shaping of the pellets produced by the wood pellet making machine is not high, scrap powder too much?
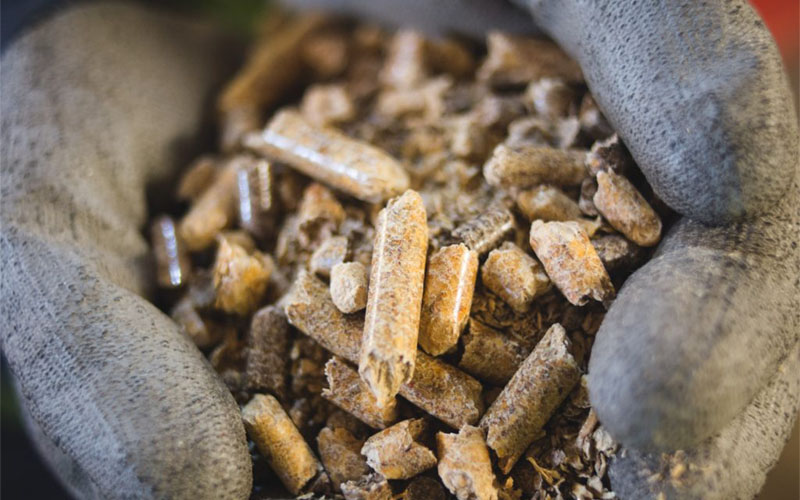
When the wood pellet making machine presses wood pellets, sometimes it will not be formed. The pellets are very loose, the pellets forming rate is low, or even the pellets are not pressed. There is also a situation where the pellets are good and the equipment output It’s also good, but the wood pellets will crack after a while. Customers should not worry if they encounter these situations, because there are many reasons, and it is necessary to investigate gradually to find the cause.
A – If it is a new wood pellet making machine, consider whether it has not been run-in with wet or oil after the purchase a wood pellet making equipment. This is a problem that many people easily ignore. If you ignore this link, it is likely to cause the wood pellet making machine to become stuffy and block the hole when it is turned on, so it is necessary to take some wood sawdust that will be compressed for the purchased wood pellet making machine, and mix it with about 10% industrial oil, such as ordinary engine oil. Knead the small pieces in the material, mix them thoroughly, put it into the sawdust pellet machine, turn on the machine to press the pellets, then put the pressed pellets back into the wood pellet making machine, repeat 5-6 times, and then put in the normal raw materials, that is Can be pelletizing normally.
B – If it is not a new wood pellet making equipment, then the following issues should be scheduled:
- The size of the particles.
- The temperature and pressure of the wood pellet making machine heating.
- Sawdust raw materials.
- The compression ratio of the wood pellet making machine ring die.
- The gap between the pressure roller and the wood pellet making machine ring die, etc.
The reason why I deformed by several common pelletizing explain in detail, we want to help our customers.
- The size of the particles. Studies have shown that in the process of biomass gasification, the smaller the size, the higher the gasification efficiency. This is because when the size becomes smaller, the gas generated inside the biomass is easier to diffuse to the surface.
- The temperature and pressure of wood pellet making machine heating. Too high or too low temperature and pressure will cause pelletizing failure, and also have an important impact on the density after molding and the effect after molding. If the temperature is too low, the input heat will be reduced, which is not enough to shape the material, and it will increase the power consumption of the wood pellet making machine. If the temperature is too high, the surface of the molding fuel will be thermally decomposed severely, cracks will appear, the strength of the molding fuel will decrease, or even the molding will not be possible. . If the pressure is too high or too low, it will directly affect the wood pellet making machine of the finished product.
- Raw materials:
- Generally speaking, soft wood such as pine wood are easier to granulate. If the raw material is too hard or the raw material is flour-like fine powder (the specification of wood sawdust is 1-2mm), then it is necessary to incorporate shavings, which is basically forming.
- Moisture control: The moisture content of the wood sawdust raw materials should be controlled at about 13% (currently 8% is generally required for the moisture of the finished wood pellets in the market). Because of the characteristic hardness of the raw materials and other reasons, the specific value should be based on your actual production situation. It is concluded (the recommended moisture range is between 10-20%) that our pellet machine requires a moisture content of 13%-17% for pelletizing wood chips such as pine, fir, and eucalyptus.
- The principle of raw materials: different raw materials such as wood chips, straws, paper chips or other biomass raw materials have different properties, different fiber structures, and different degrees of difficulty in forming. Materials that are more difficult to press, such as palm fiber. There is another one, if it is a mixture of materials. If so, the mixing ratio of various ingredients will also affect the molding rate.
- The compression ratio of the wood pellet making machine ring die does not match the characteristics of the raw material: some companies think that the compression ratio is the ratio of the die hole length to the diameter of the die hole, and other companies call this the aspect ratio. Some companies believe that the compression ratio is the ratio of the square of the diameter of the horn hole to the square of the hole diameter. Either way, the compression ratio calculated will be due to the fact that after the material is squeezed and rubbed with the mold and the pressure wheel during the production process, the diameter of the hole will become larger, and the length of the die hole will become shorter, and the quality of the particles will decrease. Therefore, the compression ratio of the abrasive tool provided by the wood pellet making machine manufacturer to the user is only customized according to the commonly used materials. Therefore, customers want to find a suitable compression ratio based on their own raw materials, which requires customers to pay attention in production practice. Only in this way can we better grasp the quality of the particles and improve the working efficiency of the wood pellet making equipment.
Adjustment of the gap between the pressure wheel and the wood pellet making machine ring die: Generally, the gap between the pressure wheel and the wood pellet making machine ring die is controlled to be 0.1~0.3mm. If the gap is too large, the pressure is not enough and cannot be extruded. If the gap is too small, the density and smoothness of the backlog particles may be better, but it will increase the friction of the mold pressure wheel, reduce the life of the abrasive tool and affect the output of the wood pellet press machine.
When the new wood pellet making machine ring die is installed:
- Loosen the pressure roller adjusting bolt to adjust the pressure roller to the state where the outer surface of the pressure roller is close to the inner surface of the wood pellet making machine ring die;
- Adjust the eccentric shaft of the pressure rollers in order to make the gap between the pressure rollers and the wood pellet making machine ring die appropriate, and adjust the gap gradually.
- Just tighten the adjusting bolts. In use, the wood pellet making machine ring die is preserved at the expense of the pressure roller skin, because the price of the wood pellet making machine ring die is tens or even hundreds of times the price of the pressure roller skin, so the hardness of the pressure roller skin cannot be too high when a reasonable gap is selected. That is to say, the wear resistance of the pressure roller skin cannot be higher than the wear resistance of the wood pellet making machine ring die. (Of course this is provided to you by the wood pellet making equipment manufacturer, which depends on the conscience of the company) So how to judge that the gap between the ring die and the pressure roller is between 0.1-0.3 (of course this is just a data for easy description)?
Based on RICHI many years of industry experience, two people are required to work together. When the motor is clicked, it is better to hear the wood pellet making machine ring die and the pressure roller reach a state of contact and non-contact during the process of no material contact between the wood pellet making machine ring die and the pressure roller. (Non-professionals should not practice to avoid wood pellet making equipment failure!)
C – After adjustment, pay attention to the usual wood pellet making equipment maintenance. During the wood pellet production process of the equipment, the materials used must be cleaned up to avoid materials mixed with hard particles such as large sand, sand, iron blocks, bolts and iron filings. Because these inclusions accelerate the wear of the ring die, and a large number of large hard inclusions will cause the ring die to be stressed multiple times, causing the ring die to fatigue. When the force exceeds the strength limit of the ring die, the ring die will explode.
Pellet Production Line
Core Equipment of Wood Pellet Production Line
RICHI Pellet Machine For Sale
- Wood Pellet Mill For Sale
- Grass Pellet Making Machine For Sale
- Straw Pellet Machine For Sale
- Rice Husk Pellet Machine For Sale
- EFB Pellet Machine For Sale
- Organic Fertilizer Pellet Machine For Sale
- Cat Litter Pellet Making Machine For Sale
- Textile Cord Pellet Machine For Sale
- Paper Pellet Making Machine For Sale
- Pellet Maker For Pellet Stove